Fane Speaker Box enclosure design diy how to building
subwoofer box
projects loudspeaker plans
Fane Subwoofer Box Design for: Colossus.15B or Colossus.15XB or
Crescendo.15B
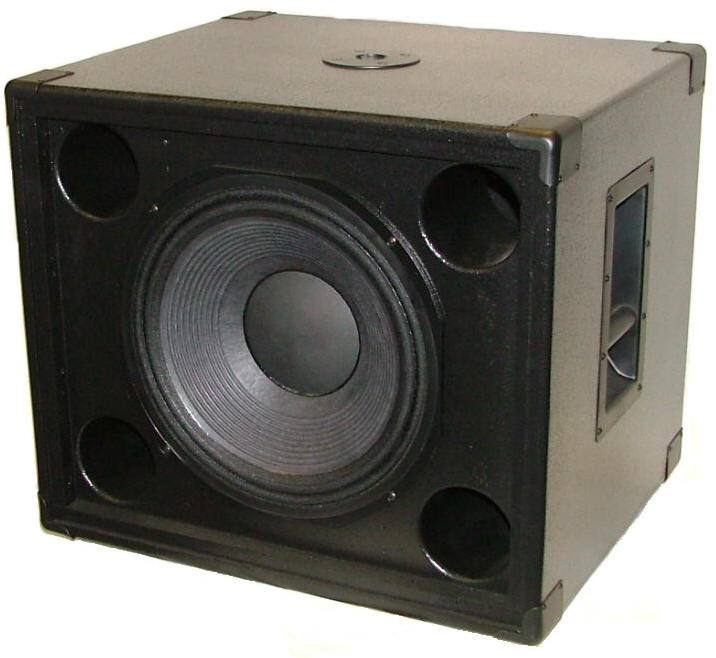
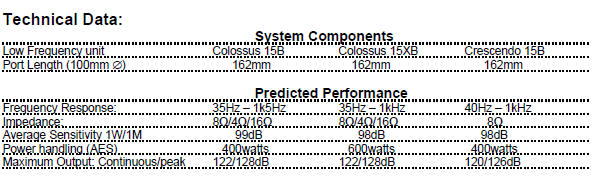 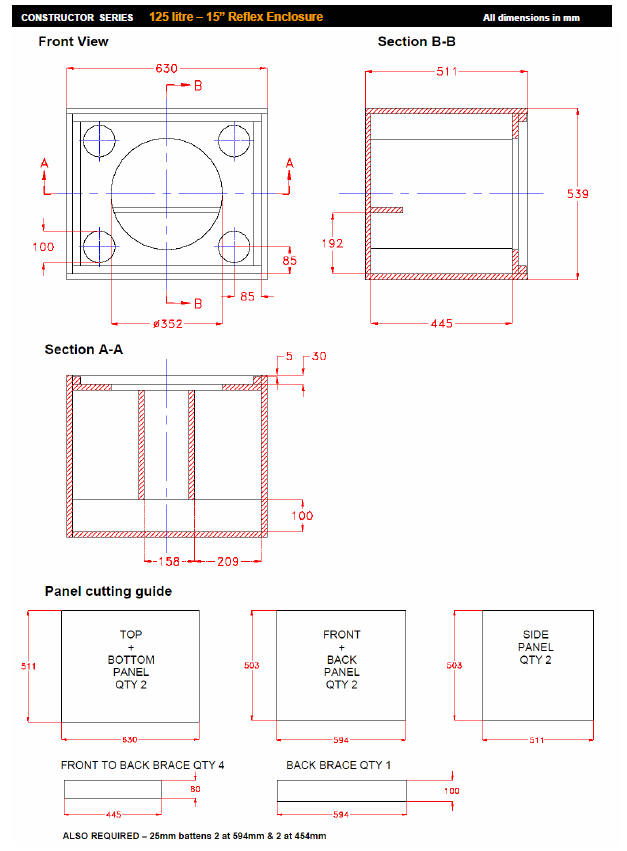
Hints and tips
Choice of timber
We recommend multi-layer 18mm Birch plywood as the best
material to withstand the rigours of intensive ‘life on the road’ or
likely exposure to damp conditions. Alternatively, 18mm Medium
Density Fibreboard (MDF) offers good acoustic properties with
the advantage of being less expensive (although heavier ), and
may be used where the cabinet will be permanently installed in a
dry environment. Both materials accept any type of paint finish
extremely well.
Construction technique
All joints should be totally airtight, liberally glued with PVA
adhesive and screwed at 200mm (8”) centres with 4.2mm or
4.8mm (No.8 or No.10) x 50 mm (2”) self-tapping screws. The
bracing panels are designed to ensure rigidity of construction,
making the cabinet as free as possible from panel resonances
caused by the internal forces generated by the loudspeaker drive
unit and resulting in unwanted vibration and colouration of the
sound. Again, these joints should be glued and screwed using
the same method.
Porting
The length of the ports as specified in the drawing should be
strictly adhered to. The cut-out size for the port is 100mm (4”).
Plastic drainpipe is ideal for this task, but as there could be slight
variations in pipe diameter we suggest the cut-out is made after
purchasing. The port when fitted should be airtight, which can be
achieved by sealing the joint with silicone sealant or polyurethane
mastic.
Acoustic insulation
To aid panel damping and prevent internal reflections and
standing waves, all internal panels of the cabinet ( with the
exception of the front baffle ) should be lagged with acoustically
absorptive material. We recommend the use of acoustic foam
wadding, glassfibre insulation or rubber carpet underlay which
should be glued, stapled or tacked to the inside of the cabinet,
taking care to ensure that port tubes are not obstructed.
Crossover network
This cabinet is designed as a passive unit, and adequate external
signal processing arrangements should be made to filter out
high-frequency signals.
Internal wiring
Wiring should be kept away from moving loudspeaker parts and
fastened to internal panelling to avoid buzzing. We encourage
the use of colour coded wiring to identify polarity (red for +ve and
black for -ve), and recommend carrying out a phase check before
first using the cabinet. This is achieved by applying the positive
terminal of a battery to the positive cabinet input which should
result in the speaker cone moving forwards if in phase (or by
using a dedicated polarity checker).
Drive unit fixing
The drive unit should be front mounted to the baffle using
T-nuts and fixing bolts, and is supplied with a length of self
adhesive foam sealing strip which should be fitted around
the front edge of the speaker cut-outs to guarantee airtight
conditions.
Loudspeaker protection
The exposed front of all speaker drive units is of course
vulnerable to damage, necessitating some means of
protection which must be robust but acoustically transparent.
Cloth/foam type grilles are feasible for fixed cabinets, but a
metal mesh grille is certainly the preferred and superior
option. It is recommended that a foam gasket material is
used between the wooden cabinet and the metal grille to
prevent any unwanted resonances.
Cabinet hardware
Handles, terminal panels, protective corners, pole mounting
accessories etc. are readily available from many different
sources.
Fane Acoustics will be pleased to recommend approved
suppliers of all associated components.
Cabinet finishing
Cabinet finishing is largely a matter of personal preference
and as such, detail of this is omitted from the drawing.
Generally cabinets are either painted or covered in carpet or
vinyl material. If a carpet material is chosen it is
recommended that a very dense tight pile type is used and
that metal corner protectors are fitted. Corner protectors will
have a defined radius that the edges of the cabinet should
be finished to. The cabinet shown on the first page of this
document has all the external edges routed with a 13mm
radius and coated in a hard wearing textured epoxy paint.
Two steel carrying handles have been fitted. There are
various types of handles and terminal panels available and
again details of these have been omitted. It is recommended
that these be purchased and cutouts be made in an
appropriate position in the panels before final build. Be
aware that handles and terminals are not necessarily airtight,
which will be detrimental to performance but can be easily
remedied using a
|